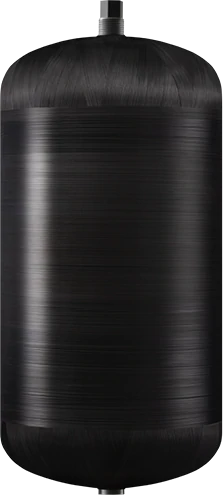
High-Pressure
Composite Gas Tanks
Light and Strong.
Our specifications assume
the harshest environments
In space, the tanks will be used for helium gas and nitrogen gas storage in rockets and satellites. On ground, the tanks will provide future solutions for ultra-high pressure hydrogen storage and transportation.
The tanks are expected to play a vital role in the future of a carbon-neutral and hydrogen society. This was even more reason for weight reduction, imperitive not only for highly reliable optimum strength and gas storage efficiency, but also from the point of material costs and handling.
30% Weight Reduction
The TYPE IV tank is developed with a resin liner, in contrast to a TYPE III tank with a metal liner overwrapped by carbon fiber. By eliminating the metal, significant weight reduction and cost savings are achieved.
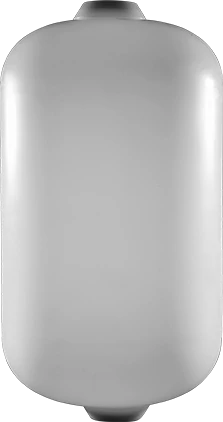
105 MPa
Design Pressure
A filament winding molding method is employed to maximize the strength of carbon fiber reinforced plastic (CFRP). Productivity significantly improves and performance of pressure resistance is maximized with only a minimum amount of winding. As a countermeasure against leaks, a special process is applied to the joint to eliminate the sealing part between the resin liner and the mouthpiece.

Linerless High-Pressure Composites
Research and development of a linerless TYPE V, the lightest composite tank, is underway targeting a further 10% weight reduction, compared to TYPE IV which has a resin liner.
CASE STUDY
H2 (Hydrogen)
Our composite tanks can be deployed as cylinder bundles onto hydrogen trailer trucks and other transfer equipment, as well as stationary hydrogen stations, and fuel cell drones.
The strength has been proven in POC demonstration* at 105 MPa design pressure and 236.3 MPa burst pressure (2.25 times safety factor) over 130,000 cycle tests at 70-90% amplitude.
※ Preparations are underway for certification from the High Pressure Gas Safety Institute of Japan.
A seamless resin liner is formed by rotational molding and fusing of the mouthpiece. Using a filament winding method, carbon fiber composite material is wound around the liner then heated and cured in a furnace. For the primary capability, the burst pressure in high pressure vessels, the tensile strength of the carbon fiber is critical and best utilizes a high specific strength.
SPECIFICATION
- CATEGORY
- CONDITIONS
- Design Pressure
- 105MPa
- Burst Pressure
- 236.3MPa(Safety Ratio2.25)
- Capacity
-
30Liter/100Liter
200Liter
- Hydrogen Permeability
- under 5cm3 / L・H
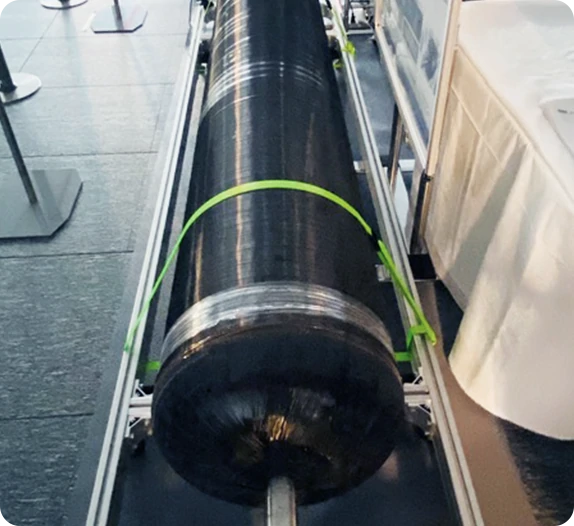
* Photo image is 300 L type
100L
*Approximate Mass: 170 kg
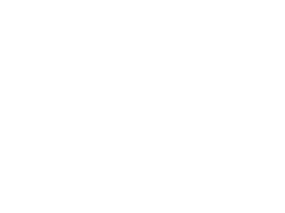
200L
*Approximate Mass: 330 kg
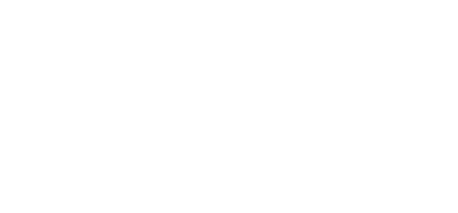
300L
*Approximate Mass: 515 kg
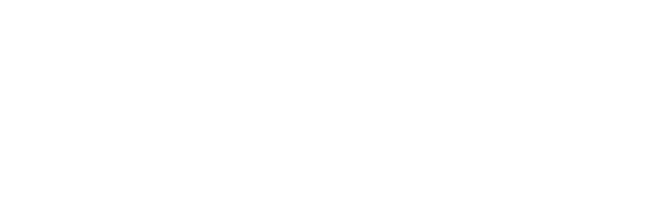